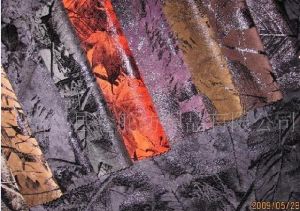
definition:
There are two types of suede, natural and man-made. This is referred to as artificial suede.
Suede
classification
Artificial suede manufacturing methods can be roughly divided into three types: woven fabrics, knitted fabrics, and non-woven fabrics.
Imitation suede fabric is a textile fabric with special style that is made of special textile raw materials and processed with special dyeing and finishing technology. It is one of the most popular high-grade fabrics in the domestic market. Imitation suede feel and appearance are quite similar to natural suede, its surface texture structure is similar to natural suede, after special finishing, fine smooth, soft and full, more durable than natural suede, but also easier to maintain . It is widely used in modern fashion, shoe materials, toys and furniture decoration. It is a novel decorative material. The suede is made of new raw material microfibers as the main raw material. After the reduction (grinding) process, it not only has the advantages of soft hand feeling, good drapability, strong stability (no shrinkage or elongation due to cleaning), but also good air permeability. Sex, pest control, anti-corrosion.
Suede - Performance and Features
Sea-island microfibers disperse a polymer in another polymer. In the fiber cross-section, the dispersed phase presents an island state, and the mother body corresponds to the sea. The island component was finally dissolved by fabric finishing to obtain ultrafine fibers having a monofilament diameter of less than 3.0 μm. The island microfibers are usually combined with high shrinkage fiber composite processing networks into different shrinkage composite fibers. Since the shrinkage of the two raw materials is quite different, after the finishing process, the fabrics form an ivy-like multi-layered structure and float on fabrics. The islands on the surface of the islands are tangled with each other like the ivy, giving the fabric an ultra-soft, delicate, smooth feel. High-shrinkage fibers shrink to become core filaments, their greater strength and stiffness, giving the fabric super-suspension performance.
Printed suede
Unique style
The fibers covering the surface of the fabric are slender and form a multi-layered structure, so that the fabric has a small reflection point, a soft luster, a soft color, and an appearance of fullness, fineness, and refinement. The smaller fiber bending stiffness makes it easier for the fabric to achieve an elegant, chic effect. The core layer is a denier high shrinkage yarn, giving the fabric an excellent drape. Visual comfort is unique.
Excellent comfort
Due to the multiple and dense fiber gaps, the capillary action can be used to make the fabric obtain better water absorption and oil absorption. The microporous structure between the fabrics allows the fabric to have more static air and therefore better thermal insulation. The fine fiber denier makes the fabric feel soft and smooth, and has obvious advantages in terms of touch and physiological comfort.
Significant waterproof transmission performance
The diameter of a raindrop is usually 100 to 200 μm, and the body's water vapor is about 0.1 μm. By controlling the shrinkage rate and changing the appropriate fiber gap, we can fabricate a sea-island high-density fabric with a gap of only 0.2 to 10 μm, achieving excellent waterproof and vapor-permeable performance.
Strong decontamination ability
Microfibers have a large specific surface area and many voids, which give fabrics a very strong cleaning effect. They have a slim and delicate fiber and protect the objects being cleaned from scratches. This is a new generation of high-performance cleaning products.
Wide range of uses
Through the design and processing of fabrics, the fibrillation characteristics of island fibers are extremely fickle, and many special fabric styles can be obtained, such as imitation cashmere, imitation suede, MOSS velvet, and ultra-high density fabrics. Such fabrics can be widely used in clothing, apparel, luggage, interior products and industrial fields.
Many of the suede-like fabrics developed using sea-island fibers are as good as natural suede, and many have even better properties than natural suede. The fabric has soft hand feeling, good drapability and light texture. It is half of the genuine leather and can be woven into fabrics of different thicknesses and weights. Various surface treatments can be performed to obtain various surface effects. The surface has a writing effect, a good three-dimensional effect; the shrinkage of the damp heat is small, has a good breathable waterproof and vapor permeability effect, and the fabric has high strength and is far superior to the natural skin.
Weaving ultra-high density fabrics, utilizing the shrinkage properties of high shrinkage yarns, weaving fabrics with higher density and higher water pressure resistance. Although the density of this type of fabric is very high, but because of the fiber is very fine, light texture, good drape, soft and full of soft and full color, the appearance of bright and warm, while maintaining considerable moisture permeability and breathability, wearing a very comfortable.
Suede - Woven Suede
Weaving with a shuttle weaving machine and then finishing after finishing.
1, the design principle
In the development of synthetic fiber suede products, the raw materials we use are the filaments of microfibers, which are woven into fabrics. After a special dyeing and finishing process, fine and uniform hairs are formed on the surface of the finished fabrics. The ultra-fine fibers have the advantages of being fluffy, elegant, and soft to the touch. The drape and softness of the ultra-fine fiber fabric are excellent and the hand feels comfortable. There are various types of microfibers, which are suitable for suede fabrics such as polyester/polyester-seafood fabrics and polyester/cotton cakes. Sea-in-the-sea fibers are opened by the dissolution method, and the orange flap fibers are opened by the exfoliation method. Dissolving polyester/polyester-in-sea fiber by dissolving method makes it more reliable to turn microfiber into ultrafine fiber after opening fiber. Therefore, we have used polyester 16.7tex/36fx371 (Island Silk) + 7.6tex conventional polyester to cover the twin strands, using polyester of 1.1etex as the raw material for the development of suede-like suede products.
The island silk is a polyester island wire of South Korea's Hui Weiss. Its single fiber ** has 37 islands. After the sea part is dissolved, the single fiber is 0.05 De. It has a powdery, soft feel and a suede-like appearance.
2, production process analysis
There are three steps in the success of the production of woven embossed suede suede suede.
2.1 The quality of raw materials and the selection of the fiber-resolving formula
The polyester island filament provided by South Korea's Huiwei Shi Company was selected. To ensure the stability of the cloth quality, it is required to ensure that the raw material is a first-class product and the same lot number. The fibrillation recipe uses a proprietary high temperature caustic water (150°C, pH=13-14 water) process recipe that matches the raw materials.
2.2 Weaving process
Before the weaving should be done evenly or coated uniformly, the vacuum degree and the process choice of raising and lowering the temperature during shaping are very important, otherwise, the coloring phenomenon of the fabric is likely to occur after dyeing.
2.3 Grinding, dyeing and sueding
Bad results will produce deep, light colors. The buffing of the fabric is done through the cutting of corundum. The number of sand pits is small and the corundum particles are large. The force acting on the fabric during the grinding process is large, the milled hair is longer, and the strength of the fabric is also decreased. If the number of sand skins is too large, sanding is more difficult and the cost is increased accordingly. According to the sanding mechanism, we adopted the “first heavy and light†sanding process for the five sanding rollers, that is, the first sanding roller uses the lower mesh sand belt. The purpose is to cut as many fibres as possible into single fibres in the yarn; the last four rollers use a relatively high number of sand belts in order to continue to pull the fibres out of the yarn and cut them. It is important to grind and pull the cut single fiber into fluff. This will make the fluff after grinding reach the “fine, short and dense†effect better. The tension during dyeing is also very important. If the tension is too large, hair loss will occur, such as the shape of a chicken claw.
The suede treatment is mainly suede soft treatment, and the treatment of the suede directly affects the fabric's hand feeling and taking performance.
Woven suede products are mainly divided into warp and latitude suede. The zonal suede product specification is 15×5×33 and the raw material specification is 75D×225D. It can be produced both on water jet loom and air jet loom. The product is characterized by a good velvet feel, softness and fineness. The blank width is 160cm and the finished width is 145cm. Its finished fabrics weigh up to 160 grams per square meter. Woven suede is the ideal fabric for making home textiles and shoes. The longitudinal suede product specification is 11.5*5+28 and the raw material specification is 105D x 150D. It can also be produced on water jet looms or air jet looms. Its texture is better than that of zonal suede. Its strong and thick velvet feel is its main feature. After finishing, it can be used for bronzing, embossing, punching and printing. The white breadth of the product is 160cm, and the width of the finished product is 152cm. The finished product fabric weight is 170g/m2. The suede not only produces sofa sets, upholstery cloths, ladies' spring and autumn clothes, but also can make curtains after printing.
Suede - Knit Suede
Knitted suede is divided into two categories: weft knitted suede and warp knitted suede.
Knitted suede warp suede
The warp suede suede is mainly composed of an extension line of the front comb, and the extension line forms short, dense, uniform, and homogeneous fuzz through processes such as raising, dyeing, shearing, and grinding. If the extension line is too long, although it is easy to fluff, but the fluffing is too long, the cost of the product is affected, and the body bone of the finished product is not ideal. Therefore, in the design, it should not be mandatory for easy fluffing. Instead, it should start from the requirements that are conducive to the production of short, dense fluff, and select the appropriate pile needle organization. The length of fluff is preferably 0.1 to 1 mm. When it is shorter than 0.1mm, it is easy to expose the bottom, which may damage the appearance of the suede. If it is longer than 1mm, it is easy to get tangled.
The warp knitted suede needs to have a tightly organized structure. The ground structure can be a comb or two combs, which is actually determined according to the product's areal density and cost requirements. If there is only one comb, the selection of the ground yarn needs to take into account the shrinkage effect. After pretreatment, the fabric webs have to shrink about 35 to 45%. After the fabrics have been subjected to post-processing such as drawing, shearing, and grinding, the surface warp warp yarns are pulled off, and the ground yarns still need to maintain a certain strength so that the products meet the dress code requirements. The warp-knitted and warped flat tissues often used in suede suede are shown in Figure 1. In addition, if the two combs are reversed, it is beneficial to weaving, but the hemming property is serious, which is not conducive to napping processing; the two combs are provided with the same direction, which solves the curling and facilitates raising. At the same time, in order to make the edge more smooth, an extra spandex is added to the edge during processing.
The control of tension on the warp knitted suede fabric is very important. The control of the tension of the pile yarn and ground yarn and the choice of the finishing equipment will affect the suede effect. In terms of suede fabrics, the tension of the front comb should be small, and the tension of the back comb should be larger, but it should be selected properly. If the tension is too large, the warp phenomenon will appear in the weaving of the grey cloth; if the tension between the pile yarn and the ground yarn is close, and the shrinkage of the warp yarn and the ground warp, the raised warp yarn will form an arc on the suede surface. It is difficult to pull and polish the fabric.
Warp suede production process
The general technological process of warp suede finishing is: white blank→initial shaping→fluffing→shearing→opening fiber→staining→heat setting→smoothing→finished product inspection→scrolling.
Due to the unevenness of the grey cloth, the width of the door is not uniform, so it is necessary to perform a predetermined shape treatment before raising the hair. When the heat setting, the temperature can not be too high, just remove the various wrinkles on the cloth, so that the cloth is flat, the width It can be consistent. Otherwise, due to the influence of high temperature on the ultra-fine fibers, the structure changes and it is difficult to raise the nap. The general temperature is suitably between 155 and 165°C, and the setting temperature after fluffing may be appropriately higher, usually 185 to 195°C. The speed is over 30m/min. The grey fabric can be straightened and finished. The effect of fluffing is better and uniform. After the dyeing, the color is bright and the shade is good.
Several important finishing processes are discussed below.
Fiber opening process
Sea-island microfibers dissolve the sea components after they are made into fabrics, leaving island components to form continuous microfiber fabrics. Therefore, the solubility of the sea component is critical to the effectiveness of warp knitted suede. The dissolution of COPET in water conforms to the law of dissolution after swelling first. The composition, structure, molecular weight, and external conditions of COPET all have a certain influence on the dissolution. The effect of external conditions on the dissolution of COPET is shown in FIG. 2 . Curve 1 is the dissolution of the water-soluble polyester in hot water at 95°C. It is based on dissolution; curve 2 is the dissolution of water-soluble polyester in a 0.5% NaOH aqueous solution at 95°C. It also has a swelling and dissolution process, but it swells slowly, and finally there is residue after dissolution. This may be Due to the presence of Na+ and OH- ions, the dissolution balance of the polymer was destroyed, the dissolution rate became slower, and NaOH reacted with some of the components in the polymer to form a precipitate. Curve 3 was water-soluble poly. The ester contained 0.5% NaOH at 95°C and dissolved in 1g/L 1227 accelerator solution. Since the 1227 surfactant was added to the water, the surface of the water-soluble polyester was also hydrolyzed at the same time as the water-soluble polyester swelled. Small molecules promote the progress of hydrolysis and accelerate dissolution. And according to different conditions to adjust the percentage of NaOH to control the dissolution rate.
The fibrillation process is carried out in an alkaline solution, which is advantageous for the complete dissolution of the sea component, but it also has a hydrolysis effect on the conventional PET island fibers. Therefore, the sea-island fiber has to reach the complete dissolution of the sea component, and its weight loss rate The ratio of the sea component is slightly larger. If the proportion of sea component is 20%, the weight loss rate of sea-island fiber is generally controlled at about 22-26%, and the sea component can be completely dissolved. General open fiber technology curve shown in Figure 3.
Dyeing process
After the fabric is opened, the fabric must be thoroughly washed before the dyeing process. The amount of water must be large. In order to fully neutralize the lye on the fabric, wash it in a solution containing acetic acid (1g/L) at 70°C for 10 minutes. Then use clean water. Rinse to a pH of 6.5-7. If the washing is insufficient, residual alkali and fiber impurities remain on the cloth, which can easily cause coloration. Dyeing process in addition to dyeing color, the fabric shrinkage has a great influence on the fabric density and subsequent processes.
Among the influencing factors of the dyeing process, the first is the effect of dyeing temperature on suede. General polyester fibers are affected by heat, and the shrinkage varies with temperature, and a significant effect can be obtained between 80 and 100°C. The dyeing temperature is 120-130°C. This is advantageous for increasing the shrinkage of the fabric and increasing the density and fluffiness.
The second is the effect of tension on the imitation of suede in the dyeing process. The ideal state of the fabric in the dyeing process is uniform longitudinal and lateral forces, but in fact, due to the longitudinal movement of the fabric in the dyeing machine, the longitudinal tension is greater than the transverse direction.
Sometimes, in order to make the fabric have a good leather feeling for polyurethane finishing, in solvent-based polyurethane finishing, the solvent has a certain stripping effect on the disperse dyes, that is, the color becomes light, and the general color difference is about 0.5 to 1.5 grades. Therefore, in determining the color and dyeing process, can be increased on the basis of the normal amount of 5-10%, in addition to strictly control the heating rate (60 ~ 130 °C), the holding time of not less than 45min, the best is 60min. Water-soluble polyurethane resins can now be used for finishing.
Grinding process
The brushing and finishing process is to form a suede warp-knitted grey cloth under the control of a certain tension, pressure and feed speed into the ground area. Under the action of the high-speed rotating sand roller or belt, the fabric picking surface coil breaks and forms. Has a directional layer of fluff. Roughing is an important processing procedure for the production of suede-like suede, which has a great influence on the simulation of fabric suede. The length and coverage density of the fluff are mainly affected by the following six factors: the length of the front backing yarn, the speed of feeding, the speed of the sanding roller, the contact between the fabric and the sand roller, and the shape and specification of the sandpaper sand The distance between the pressure roller and the sand roller.
Warp knitted suede performance
Test project test results
Knit suede
Air permeability, mm/s 64.70
Breaking strength, N 282.20
Elongation, % straight to 19.88
Landscape 12.56
Elastic recovery rate, % straight 54.48
Lateral 36.30
Color fastness to wash as it is 4-5
White cloth stained 4
Perspiration fastness 4-5
White cloth stained 4
Rubbing fastness dry friction 4
Wet motor 4
There are many factors that affect the performance of suede products. Among them, fiber diameter, fiber type, tissue structure, and type of finishing agent are the main factors. The process parameters associated with these factors are determined based on the end use of the product.
The types of fibers currently used in suede fabrics are mostly seaweed type microfibers of Quandi. Microfiber not only maintains the excellent properties of ordinary chemical fiber, but also has a soft hand feeling, good drape, and a good effect of imitating silk. It is suitable for grinding and processing, and has good comfort. The simulation effect of suede made of microfiber is best. .
The size of the machine number should be selected according to the actual use. For example, the machine number used by the majority of the current manufacturers, E28 imitation suede fabric is loose, feel soft, suitable for direct fabric, E32 fabric is relatively close, feel relatively Hard, suitable for composite fabrics.
Judging from the organizational structure of the fabric, warp knitted suede is more similar in structure to natural suede, and the resulting product has better hand and performance.
The fiber-opening process is an important post-finishing process for the imitation of suede. In order to completely dissolve the sea component in the sea-island type microfiber, a certain amount of hydrolysis accelerator can be added, and the weight loss rate of the fiber should be controlled to the sea component. The bigger one is better.
Weft knitted suede
(weft suede) is a type of knitted suede. More common on the market are radial suede and zonal suede in warp knitted suede and woven suede. Weft-knitted suede is an emerging product. Currently, there are not many manufacturers and the demand is not large. The manufacturing process is more complicated and troublesome.
Weft-knitted suede can be subdivided into two types: ordinary weft-knitted suede and four-faced bomber suede. Ordinary weft-knitted suede has elasticity in the weft direction, and all-in-one elastic suede has elasticity in the latitudinal direction.
Compared to other suede varieties, weft knitted suede has good elasticity and soft touch is its main advantage. At present, foreign countries are mainly used for sofa covers, gloves, clothing and so on. The general grammage ranges from 120g/m2 to 260g/m2, with the width ranging from 150CM to 160CM.
The raw material for weft-knit suede is mainly island silk. Island silk is a very rare and precious microfiber, and there are only a handful of domestic manufacturers. Generally used for weft-knitted suede is 105D. After the island silk is formed by a large circular knitting machine to form a suede fabric, the suede fabric at this time has no sense of feather and no color, and it needs to be subjected to a plurality of processes such as dyeing and grinding. The final result is a hairy, elastic weft-knit suede.
Imported German big round machine weaving weft knitted suede, good elasticity, fine feeling, feel comfortable. This fabric is made of imported high-shrinkage raw materials from the island. Its production process is complex and its effect is good. Mainly used in home textiles and clothing, after bronzing, compound and other finishing, has a very good market prospects. New elastic weft knitted suede (all islands) series. This fabric has fine texture, elastic retracting effect and comfortable feel. Specifications: Island superfine high shrinkage fiber 105D * 105D, the surface for the effect of the two kinds of brushing and grinding effect, the finished product width is generally 150cm-155cm, the finished product weight can be done according to customer needs: 140g/m2-220g/m2 One-sided style and double-sided style.
Suede - Development Trends
Suede includes cowboy faux suede, warp-like suede, weft-like faux suede, warp-knit suede, double-hide faux suede, and stretch-faux suede. Suede fabrics have many properties and no less than natural suede, and many of them are even better than natural suede. For example, their fabrics are soft, velvety, drape, and light and thin. The current market is a market that emphasizes innovation. Whether it is apparel fabrics or home textiles, it is in the midst of this ever-changing change. Ordinary mass fabrics are no longer a concern in this innovative market because it is too common, and innovative fabrics have begun to sing the protagonist of the fabric market.
Embossed warp suede
This is a casual fabric that is favored by women. The surface of the product is made of island silk DTY75D/36F*37 islands, and the base yarn is made of polyester FDY50D. It is made by weaving plain weave on high-speed warp knitting machines. Has been pre-shrinkage, stereotypes, dyeing and other sophisticated technology from processing. The width of the fabric is 150cm, and the weight per square meter is about 140g. The current wholesale price on the market is 18.00 yuan per meter. Because the fabric is embossed and finished, the style of the fabric is more vivid and vivid, and the biggest advantage is that it has a soft touch, good drape, good taking, and easy care. These are all inferior to other velvet cloths. Currently, there are nearly 20 kinds of irregular embossed patterns, such as irregular square dots, leaves, daffodils, corrugated, rose, and Chinese rose. From the perspective of color, pink, sky blue, light blue, light gray, and coffee are also quite popular with customers. . Due to the large number of fabric patterns on the cloth, the background is colorful and can meet people's different needs. This cloth is an ideal fabric for casual wear and skirts for young women. After being fitted into the upper body, it is both stylish and elegant, and adds attractive charm.
Zebra Strip Suede
It is understood that the new product adopts seaweed composite yarn 105D and polyester DTY200D/96F as raw materials, weaving on the water jet loom by using stripe weaving, and it has been finished through multiple dyeing and finishing processes. Its fabric width is 150cm, weighing about 180 grams per meter, the current wholesale price per meter of finished products on the market in the 19 yuan, belonging to the high-end fabrics. Zebra strip suede raw material combination is reasonably reasonable in place, soft to the touch, good color fastness, durable wearable, comfortable to wear, good taking and other advantages Bo, style trendy, these kinds of advantages won the trust of consumers. At present, the colors on the market are popular with merchants such as Tibetan blue, beige, light gray, rose, beige, coffee, bronze, and purple. And the fabric also has an advantage is not only the ideal fabric for young men and women casual wear, but also the preferred home textile fabrics, such a fabric into the upper body, not only beautiful and comfortable, but also to make the youthful vitality. Related people are still quite optimistic about the market outlook for this cloth.
Laser Bronzing Suede
The fabric warp yarns are made of polyester DTY75D/72F, the weft yarns are island composite yarn 225D, and the fabrics are made of five tissue structures and interweaved on a water jet loom. After weaving the gray fabric by slack scouring, desorption, water absorption, predetermined, alkali reduction, dyeing, and then using laser gilding finishing process, the final finished product. Its fabric width is 150 cm, and its weight per metre is about 180g. This fabric has a novel pattern, dazzling fabrics, dynamic, and also meets the requirements of environmental protection. “Differentiation of raw materials, functionalization, novelty of structure, and new style†are the best interpretations of this new product. The fabric can be widely used in sofas, bags, automotive interiors and other aspects, the current demand for home textiles category still prevails, mainly sold to Shanghai, Guangdong, Shandong, Liaoning, Zhejiang, Fujian and other places.
Bamboo suede
This is a favorite home textile fabric, is also a rising star of chemical fiber island silk fabric. The fabric warp uses DTY75D wire, the weft yarn adopts island composite yarn 105D+ special yarn, and weaves fine woven tissue weaving on the water jet loom. The fabric width is 160cm, and the transaction price of the current gray fabric is about 7.50 yuan per meter. Due to the ingenious combination and combination of raw materials, the cloth surface presents an irregular distribution of "bamboo joints" with a hemp fabric-like style that gives the cloth a bamboo-like stylistic effect, which is the most characteristic of this fabric. The fabric is favored by various consumers for its advantages of soft hand, bright luster, unique style, novel appearance and rich colors. In addition to some fabrics used to make clothing, the fabric is widely used in sofa fabrics, sedan covers, etc. after being compounded by T/C fabrics. It is popular among many merchants, and the sales situation is in full swing.
Scarves in the era of our emperor Chiyou, is that those skins were hunted, as prizes issued to those who are worthy of people, that is, the initial scarf of this product not only for the emergence of the physiological needs of warmth, but a Kind of spiritual comfort. Today's scarves have become all human needs, people in cold areas use it to cold and cold, people in the desert use it to prevent wind and sand, where people do not have scarves scarves, the original is to dress up the United States. So it has become an indispensable necessity for everyone in the world.
With the development of the times, scarves have been infused into the elements of different cultures all over the world, becoming different materials and different forms appear in our lives. Such as: strip, triangle, square, etc .; wool material, chiffon material, silk material, linen cloth, fabric. As a civilized product of China, silk was exported overseas long ago. Hardworking Chinese made many products using traditional handicraft silk, including embroidered scarves. Aishe embroidery as a folk technology industry, we have pure hand embroidery, embroidery silk scarf, it is to the extreme development. Embroidered twins with different embroidery habits, scarves inlaid with different patterns, it seems that each of our products are full of charm, coupled with silk is a natural animal protein fibers, smooth and soft, shiny, with warm winter Cool feeling; but also effectively to avoid sandstorms. Silk scarves are expensive fashion items, but also a gift of high-level gifts. Mrs. Peng Liyuan, the wife of Chairman Xi, also often wears embroidered scarves and gives it to some visiting guests as a gift.
Hand Embroidered Scarves,Big Size Hand Embroidered Scarves,Long Hand Embroidered Scarves,Lady Hand Embroidered Scarves
Haiyuan Aisha Handicrafts Company Limted , https://www.nxembroidery.com